When
a customer buys our tubing we want them to be able to start utilizing
it right away. One large difference between us and our competition
is that we make it easy for you to learn the basics of cutting
and bonding even before you buy from us. We realize that a little
customer service can take us far with our customers. This is why
we published our cut and bond page. We plan plan on contributing
to this page on a regular basis to give you the inside scoop on
working with this specialized material.
SIMPLE
CUT AND BOND GUIDE
-DISCLAIMER-
The purpose of this
bonding guide is to explain the basics of bonding carbon fiber
tubing. Any information contained in this guide should be considered
a recommendation only. Due to the wide variety of loading scenarios
and application conditions CarbonFiberTubeShop.com (Ultra Carbon
Fiber) accepts NO liability for any injury, loss of life, or damage
to property caused by following the instructions in this guide.
You are ultimately responsible for making sure your project is
safe and successful. When building structures with our tubes you
are responsible for obtaining suitable engineering guidance to
ensure that an appropriate factor of safety is met. With that
out of the way let's get started with our bonding example.
STEP
1: The first decision you face when bonding tubes together
is which adhesive to use. There are many variables that must be
accounted for before you select an adhesive for your project.
These may include but are not limited to the temperature range
in a given application, chemical exposure if any, and weather
exposure. For this test we have selected Loctite 9430 as shown
in the image below. This is a room temp curing, two part epoxy
designed for structural bonding. We chose this epoxy due to it's
high peel and shear strength coupled with it's resistance to environmental
factors. You can view the the technical document published by
Loctite here.
This epoxy is easy to use but has a cure time of about 5 days.
You may also oven cure this epoxy for faster cure. Please read
the entire technical document before moving forward. We suggest
you print it out at this point so that you may refer back to it
later on.
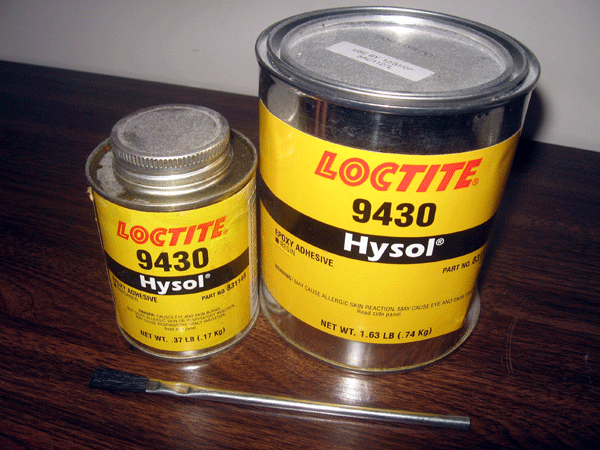
STEP 2: Here are the 3 tubes
that will be bonded. The inner ferrule has been cut so that about
3" of the ferrule will be bonded into tube A and 3 inches
will be bonded into tube B. In this way we can take two short
lengths of tubing to create one longer tube. This ferrule has
a "0 deg" bias layup and is sanded to a tolerance that
will provide a proper bond gap. A bond gap is the difference between
the OD of the inner ferrule and the ID of the outer tube divided
by two. Here is a diagram that shows what a bond gap is:
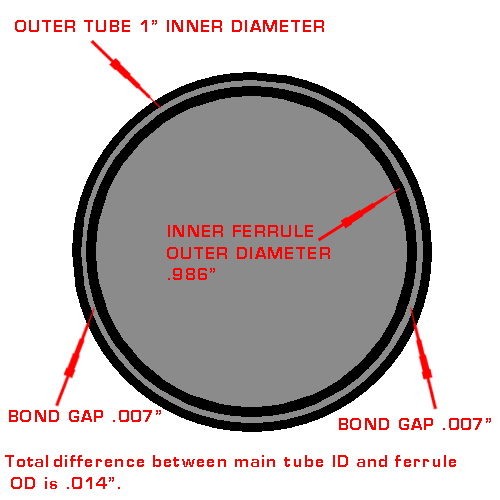
With this epoxy and our carbon tubing the minimum bond gap is
about .007"-.008" and maximum .015"-.016".
The bond gap will effect the strength of the bond and must be
tested for your application. The bond gap may be different if
another adhesive is used. If a larger bond gap is used you may
want to use a bonding fixture to ensure you have a concentric
bond gap. Some other methods of obtaining a concentric bond gap
are gauged wire wrapped around the OD of the inner ferrule tube
or you can mix a small amount of properly sized glass microspheres
into your resin prior to bonding. This ensures you have an equal
amount of adhesive filling the bond gap. The issue of a concentric
bond gap may become more critical when bonding dissimilar materials
together such as aluminum and carbon. When two dissimilar materials
remain in contact, in some environments galvanic corrosion may
become a problem if the two materials are not kept out of contact.
A concentric bond gap may be used to keep the materials from touching
as well as very thin fiberglass veil.
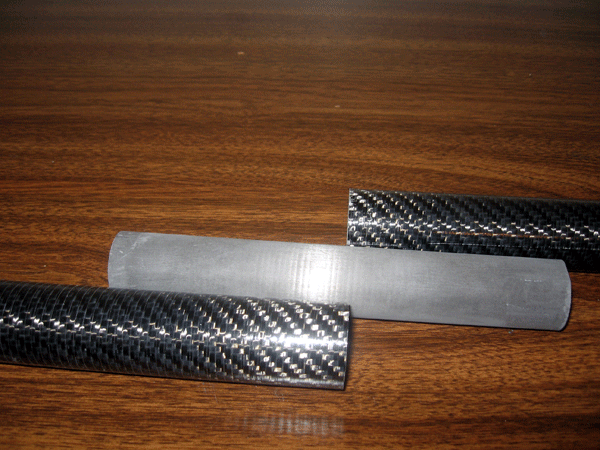
STEP 3: After we have all
of the tubes sized to a correct dimension for bonding we can start
to prepare the inner diameter of the tubes for bonding. Prior
to molding a tube on a metal mandrel the mandrel must be seasoned
with a mold release chemical. This release chemical allows the
carbon tube to separate from the mandrel after the tube is cured.
Without this chemical the tube would stick to the mandrel. We
need to remove this release chemical prior to bonding. The image
below shows a tube that has not been prepped.
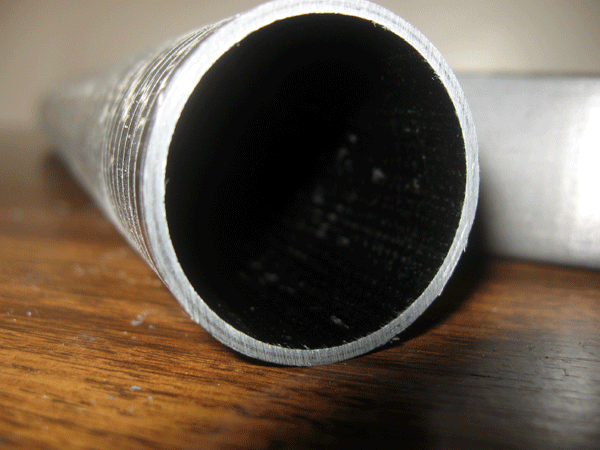
There are several methods
of preparing the main tube inner diameter. The easiest method
is to sand the inner diameter with 150-220 grit sandpaper until
the release chemical has been removed and the surface properly
abraded. Removal of the release chemical is your first priority
but the tiny scratches introduced by sanding also increase the
effective bonding area slightly which will in turn increase the
bond strength. You should avoid abrading too much because sanding
too deeply will start tearing into the carbon fibers which will
begin to weaken the tube. You should abrade to the point where
your sanding dust starts turning black. You should abrade the
surface as uniformly as possible.
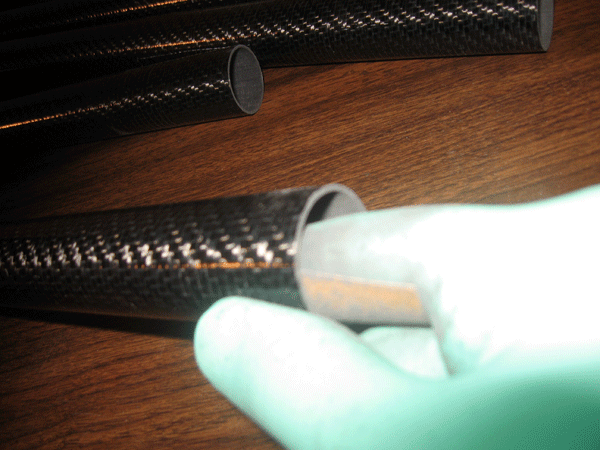
This is what your tube should look like if you're using sandpaper
to abrade the tube. Notice the scratches in the surface are variable
in their direction. Verify that you have abraded deep enough into
the diameter of the main to tube for the bond depth of the inner
ferrule at this point. The ferrule tube outer diameter will be
bonded into the main tubes and should be abraded in the same manner
as the inner diameter of the main tubes.
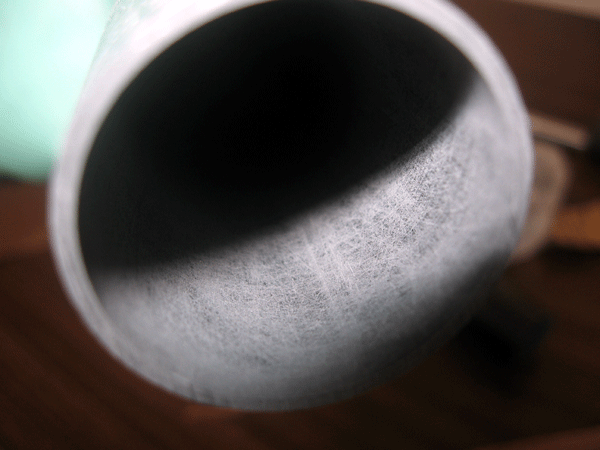
STEP 4: Now it's time to clean the surface of
the tubes. We recommend cleaning the tube first with water and
a low lint paper towel. Once the surface is free of dust you can
perform a water break test. This test will verify that you have
removed the release chemical on the inner diameter of the tube.
To perform the test just wet out the abraded surface and watch
how the water acts. The water should appear to wash out. Any beading
means the surface is not free of contamination (release chemical).
The tube should be completely dry before you degrease the surface.
Make sure all the tubes to be bonded are ready for this step so
that you don't contaminate any clean tubes with more sanding dust.
Put on some clean latex gloves and start to degrease every surface
to be bonded by wiping with Acetone. Acetone will remove the oils
that may have transferred from your skin. Do not skip this step!
Even if you have washed your hands they still have oil on their
surface. Keep degreasing the tubes with a white lint free cotton
towel or paper towel until you don't see any black dust on the
towel or at least the dust you do see is very minimal. Now set
the tubes in a clean place. If you are bonding aluminum inserts
to the carbon tubes you should bond immediately as some metals
develop a film after you abrade them. If you will be prepping
and bonding a lot of tubing you may want to buy one or more flexible
cylinder hones. Cylinder hones come in a variety of sizes depending
on the tube diameter you are prepping. Cylinder hones have carbide
abrasive embedded in balls at the ends of flexible plastic spindles.
As a result, they remove material rapidly and leave a smooth,
even finish. These tools are available through many online tool
resources and cut down on the prep time quite a bit.
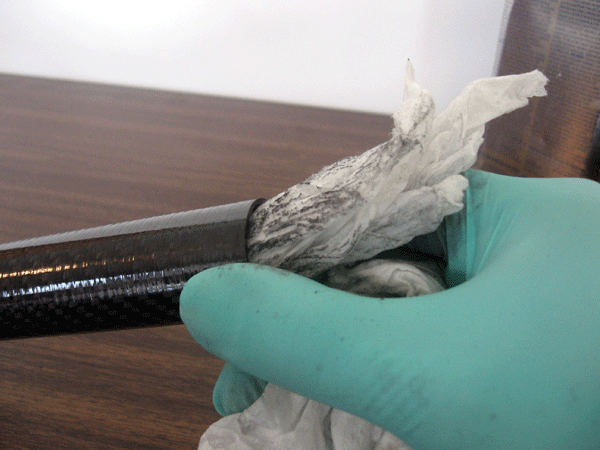
STEP 5: Now it's time to mix up your resin and
hardener. Mixing resin doesn't not need to be a complicated process.
You will need a plastic or paper mixing cup with a flat bottom
as well as a flat plastic mixing stick. A wooden tongue depressor
or plastic butter knife will work fine. You also need a scale
that measures in grams. These can be purchased at online or at
any big box store. If it doesn't measure in grams it won't work.
If you haven't done so already please read the Loctite
Techincal Document for Hysol 9430. When you're ready,
turn your scale on and and make sure it is zeroed out. Now set
your empty mixing cup on the scale. If your scale has a tare function
hit that button and you should be at zero again. Even though the
cup has insignificant weight it's a good idea to get into the
habit of mixing correctly. Now pour enough resin (in the larger
can) into the mixing cup to meet the needs of the job. Hysol 9430
needs to be mixed at a ratio of 100 parts resin to 23 parts hardener
by weight for best performance. This means if you pour in 200
grams of resin you will need to follow that with 46 grams of hardener.
After you pour the resin into the cup write the number down and
tare the scale again and pour in hardener to the correct weight.
Once you have the correct proportions in the cup you can start
to mix the two parts together. At 77 deg F you have a 50 minute
pot life or working time. This estimate is based on 250 grams
of mixed resin. If the temperature is higher or the resin weight
is greater than 250 grams your pot life will start to decrease
so keep that in mind while you're working. Cooler temps will result
in a longer mixing time and vice-versa. Mix the resin for 5 minutes
or longer if needed to achieve a uniform mix. Every once in a
while scrape the bottom and sides of the mixing cup with your
stick. After you scrape the bottom and sides of the cup wipe your
mixing stick on the rim of the cup. If you do not scrape the sides
and bottom of the cup you could end up with an incorrect ratio.
Keep your mixing slow and direct so that you don't whip too much
air into your resin. Once the color and viscosity of the resin
and hardener look uniform you are ready to bond.
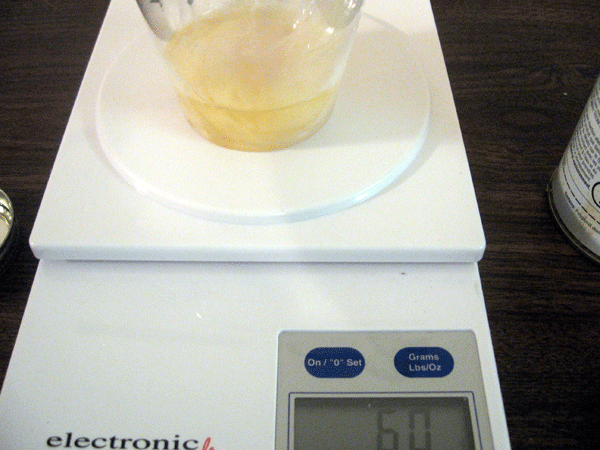
STEP 6: With a short resin brush apply a thin
layer of resin into the inner diameter of the main tubes. Do not
paint too much resin into the ID because it will be pushed back
when the ferrule is pushed into the tube. This will increase the
weight of the finished structure which is not what we want. Run
your brush over the same areas a few times to make sure the resin
finds it's way into all those little scratches you made while
prepping the tube.
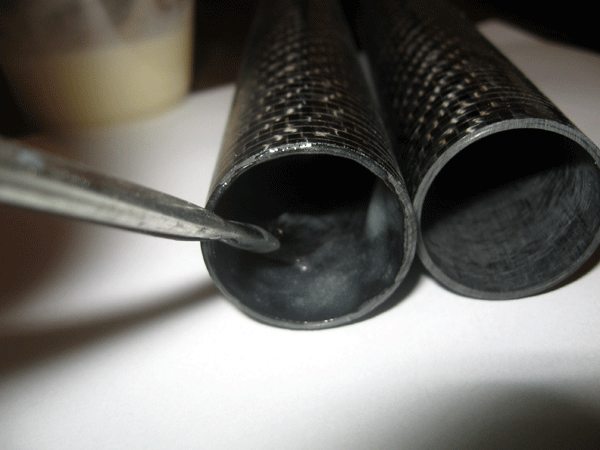
Now brush some resin on the OD of the ferrule, most of this resin
will squeeze out when the ferrule is pushed into the main tube.
Keep the other side of the ferrule free of resin at this point
so you have something dry to hold on to.
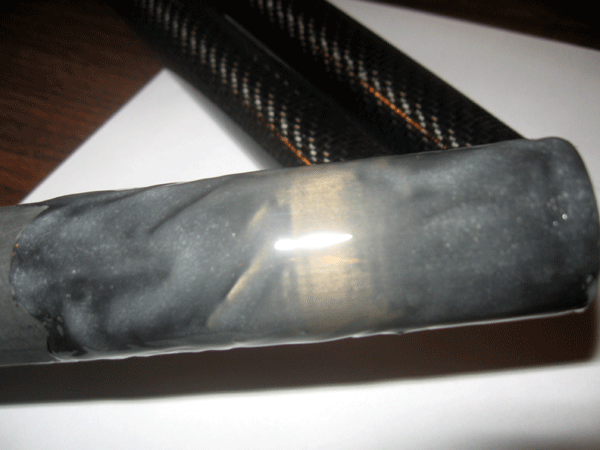
Now slowly push the ferrule into the main tube to the point required.
Give the tube a slight twist as you are pushing the tubes together.
You can use a silver Sharpie to mark the bonding depth. Do not
push the pieces in quickly Make sure you have something under
the assembly to catch the squeeze out. This picture illustrates
how little resin is actually in our bond gap.
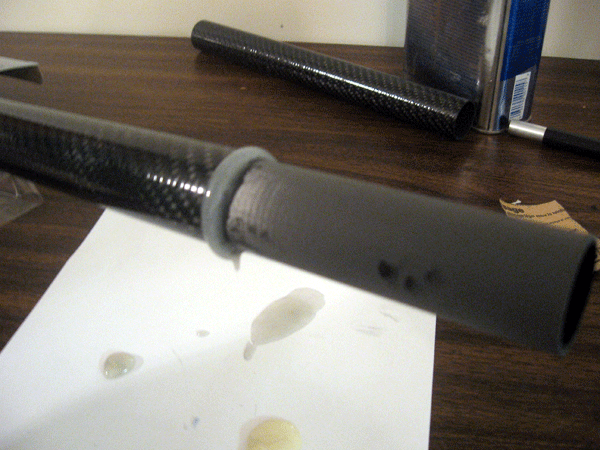
Once you are satisfied with the bond depth you can brush resin
onto the other side of the ferrule. Keep a spot large enough for
your finger free of resin so that you can hold the ferrule in
place as you press main tube B over the exposed end of the ferrule.
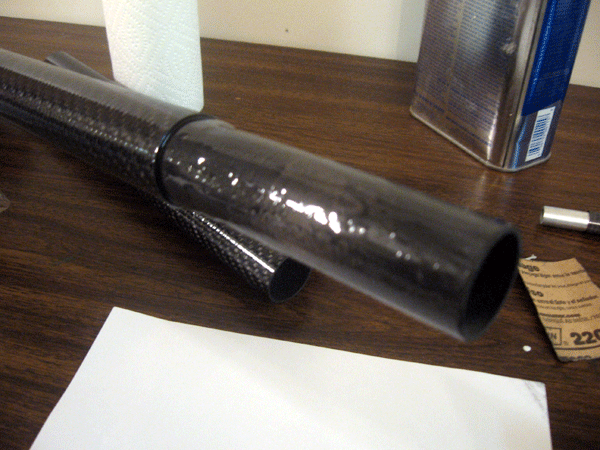
As you push the tubes together take advantage of that dry spot
and make sure the ferrule doesn't move as you press the other
main tube down the ferrule. You want to make sure you have about
the same length of ferrule in each tube. Once you get to the point
where you have no more room for your finger you can slowly twist
and push the two tubes together. If you are gentle you will see
get little movement of the ferrule.
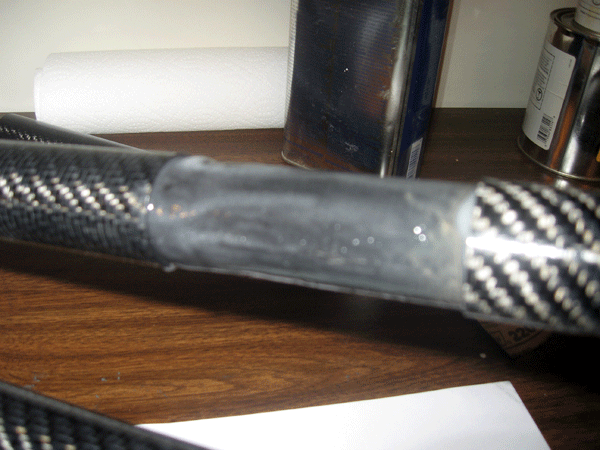
Below you can see the remaining resin squeeze-out taking place.
Once the tubes are butted up against each other you can wipe off
the excess resin with a dry paper towel. When this is done pour
some acetone on a paper towel to the point where the paper towel
is just barely damp with solvent and clean off the rest of the
resin so you have a resin free bond area. DO NOT
pour acetone over the areas itself or it will weaken the resin
around the tube joint. Once epoxy has cured you cannot clean it
with any type of solvent so make sure you clean it up now. This
goes for anything in your work area that may have resin on it.
Get it off now or it won't be coming off without sanding. In general
epoxy is very tough and bonds well to many surfaces.
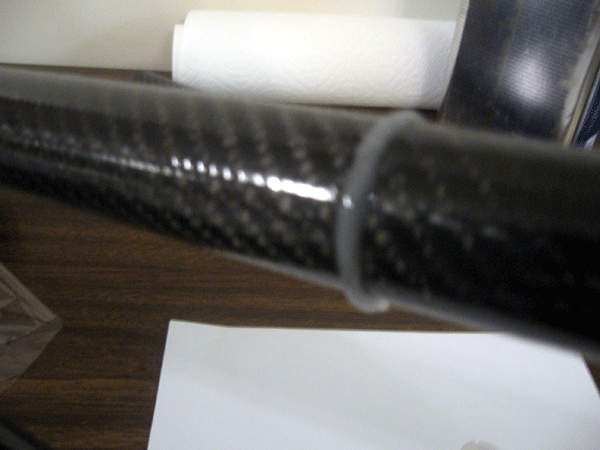
Now you should fixture the tubes together while the assembly cures.
As noted on the Loctite document this resin will take up to 5
days to fully cure at room temperature so make sure you don't
have a deadline that is is coming up sooner than 5 days. If you
have access to a heat source you can decrease the cure time. We
used a simple bungee strap on either side of the tube to keep
the pieces clamped together but there are many ways to fixture
an assembly. Also note that the gap is barely visible and the
weave pattern is matched in the image below. You must have a square
cut on each tube to avoid a large gap where the tubes butt up
against one another. That's it!
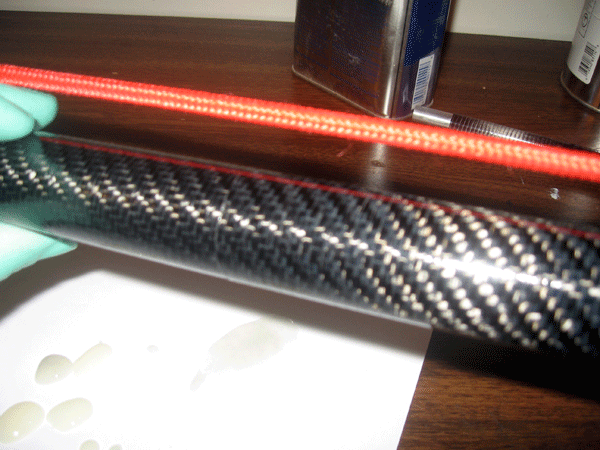
We hope that this bonding guide has been helpful to you. We wish
you success with your project and we are happy to answer any questions
that may come up at sales@carbonfibertubeshop.com
Please remember that we can handle any bonding for you at a cost
of $45 for the first bond and $10 for each additonal bond.
|